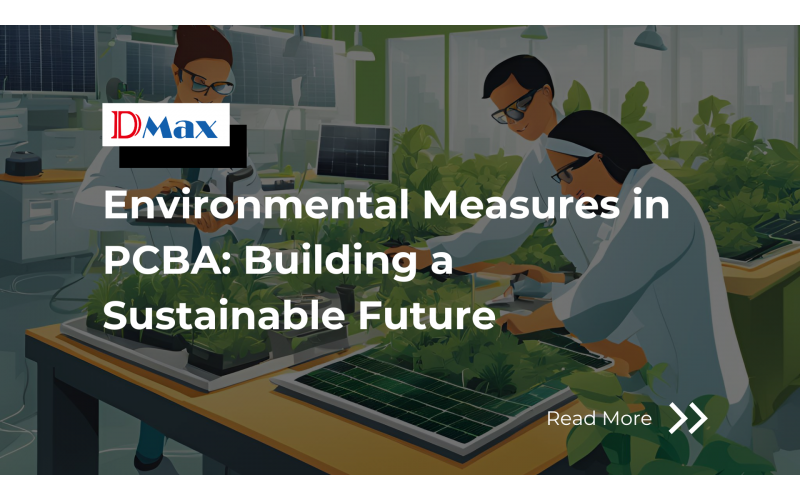
-
2025Jan
-
Environmental Measures in PCBA to Build a Sustainable Future
Why Environmental Measures Matter in PCBA Manufacturing
-
Regulatory Compliance
Governments worldwide enforce strict environmental regulations, such as RoHS (Restriction of Hazardous Substances) and WEEE (Waste Electrical and Electronic Equipment), to minimize hazardous waste and ensure responsible production.
-
Corporate Responsibility
Modern consumers and businesses value sustainable practices, making eco-friendly manufacturing a key differentiator in competitive markets.
-
Long-Term Cost Savings
Reducing waste, recycling materials, and optimizing processes not only benefit the environment but also cut costs over time.
Key Environmental Challenges in PCBA Manufacturing
-
Use of Hazardous Materials
PCBs often require materials like lead, mercury, and other toxic substances, which can harm the environment if not managed properly.
-
High Energy Consumption
Processes like soldering, etching, and reflow ovens consume significant amounts of energy, contributing to carbon emissions.
-
Electronic Waste
Discarded electronics and manufacturing by-products contribute to global e-waste problems, requiring proper recycling and disposal measures.
Environmental Measures in PCBA Manufacturing
-
Compliance with Environmental Standards
DMax ensures all materials and processes comply with international standards such as RoHS and REACH, eliminating harmful substances like lead and cadmium from production.
-
Waste Management and Recycling
We implement recycling programs for scrap materials, including copper, plastic, and solder paste, reducing landfill contributions and reclaiming valuable resources.
-
Energy-Efficient Processes
DMax invests in energy-efficient equipment, such as low-power reflow ovens and automated assembly lines, to minimize energy consumption during production.
-
Eco-Friendly Materials
Using sustainable substrates like biodegradable PCBs and water-based flux reduces the environmental impact without compromising quality.
-
Sustainable Packaging
For shipping PCBA products, DMax utilizes recyclable and minimalistic packaging to reduce waste.
-
Carbon Footprint Reduction
Partnering with local suppliers when possible minimizes the carbon footprint of material transportation, and adopting renewable energy sources further reduces emissions.
DMax's Commitment to Sustainability
As a contract manufacturer, DMax aligns its environmental measures with client requirements while maintaining flexibility in design and production. Our green initiatives not only meet industry regulations but also support clients seeking environmentally responsible manufacturing solutions.
-
Custom Solutions for Sustainable Production
We collaborate with clients to optimize designs for eco-friendly materials and processes, ensuring compliance with green certifications and enhancing product sustainability.
-
End-to-End Responsibility
From sourcing raw materials to final assembly and recycling, DMax takes a proactive approach to environmental responsibility across the entire PCBA process.
The Benefits of Sustainable PCBA Manufacturing
-
Competitive Advantage
Eco-conscious clients prefer manufacturers that share their values, opening doors to new partnerships and markets.
-
Future-Proofing Against Regulations
Staying ahead of regulatory trends ensures smooth operations without costly adjustments later.
-
Positive Brand Image
Environmental measures build trust and goodwill with stakeholders, enhancing a company's reputation.
Conclusion
Environmental measures in PCBA manufacturing are essential for a sustainable future, balancing the demand for advanced electronics with the need to protect our planet. At DMax, we integrate eco-friendly practices into every stage of the PCBA process, ensuring clients receive high-quality products with minimal environmental impact. Together, we can contribute to a greener, more responsible electronics industry.
-