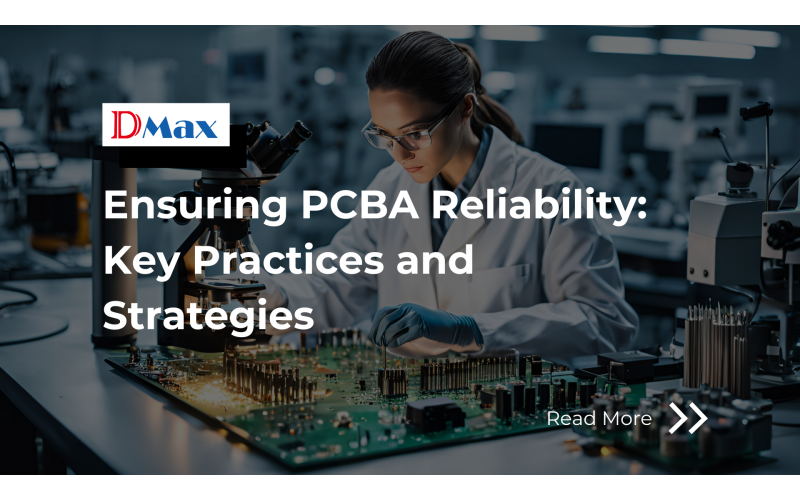
-
2025Jan
-
Ensuring PCBA Reliability: Key Practices and Strategies
Why Long-term Reliability Matters
-
Customer Satisfaction
Reliable products enhance user experience and brand loyalty, ensuring repeat business and positive reviews.
-
Safety and Performance
Failures in critical applications such as medical devices or automotive systems can have serious consequences, making reliability a non-negotiable aspect.
-
Cost Efficiency
Minimizing recalls, repairs, and replacements helps manufacturers save costs in the long run.
Factors Influencing PCBA Reliability
-
Material Quality
The choice of PCB substrate (e.g., FR4, polyimide, or aluminum) and components directly impacts the assembly’s resilience to thermal, mechanical, and environmental stresses.
-
Design Integrity
Proper layout design, including optimized trace routing, heat dissipation mechanisms, and sufficient spacing between components, prevents performance degradation.
-
Assembly Precision
High-quality soldering, accurate component placement, and robust joint integrity are critical to the functionality and durability of the PCB assembly.
-
Environmental Resistance
PCBA must withstand extreme temperatures, humidity, vibration, and other external factors depending on the application.
Strategies for Ensuring Long-term Reliability
-
Robust Design Practices
Collaborating with clients to validate designs for manufacturability (DFM) ensures optimal layouts, avoiding risks such as signal interference or thermal hotspots.
-
High-Quality Material Sourcing
DMax ensures that all materials, from the PCB base to electronic components, meet stringent quality standards and are sourced from trusted suppliers.
-
Advanced Manufacturing Techniques
Precision soldering, automated optical inspection (AOI), and controlled reflow soldering ensure consistent and defect-free assembly.
-
Rigorous Testing Protocols
Reliability testing such as thermal cycling, vibration testing, and humidity exposure ensures the assembly can endure real-world conditions.
-
Conformal Coating and Protection
Applying protective coatings shields sensitive components from moisture, dust, and contaminants, extending their lifespan.
-
Preventive Maintenance
Regularly updating and maintaining manufacturing equipment ensures consistent quality and minimizes the risk of defects.
DMax’s Approach to Reliable PCBA Manufacturing
-
Custom Solutions for Varied Applications
DMax adapts its processes to meet specific client requirements, whether the PCBA is destined for consumer electronics, industrial equipment, or mission-critical systems.
-
Comprehensive Testing Capabilities
DMax integrates in-house testing methods, including AOI, X-ray inspection, and functional testing, to detect and address potential issues before product delivery.
-
Expert Consultation
Our engineers collaborate with clients to address potential design vulnerabilities and recommend reliability-enhancing measures tailored to their applications.
Applications that Demand High Reliability
-
Automotive Electronics
Engine control units (ECUs), sensors, and infotainment systems require robust PCBAs that withstand extreme conditions.
-
Medical Devices
Life-critical applications like pacemakers or diagnostic tools demand exceptional reliability and precision.
-
Aerospace and Defense
PCBAs in these industries must operate flawlessly under extreme stress and varying environments.
-
Industrial Automation
Machinery controllers and sensors depend on durable PCBAs for consistent performance in high-stress environments.
Conclusion
Ensuring the long-term reliability of PCBA is a multi-faceted effort that combines design excellence, quality materials, advanced manufacturing, and comprehensive testing. At DMax, we are committed to helping clients achieve durable and dependable PCBAs for diverse applications. By choosing DMax, you’re partnering with a manufacturer dedicated to delivering quality and reliability, ensuring your products stand the test of time.
-