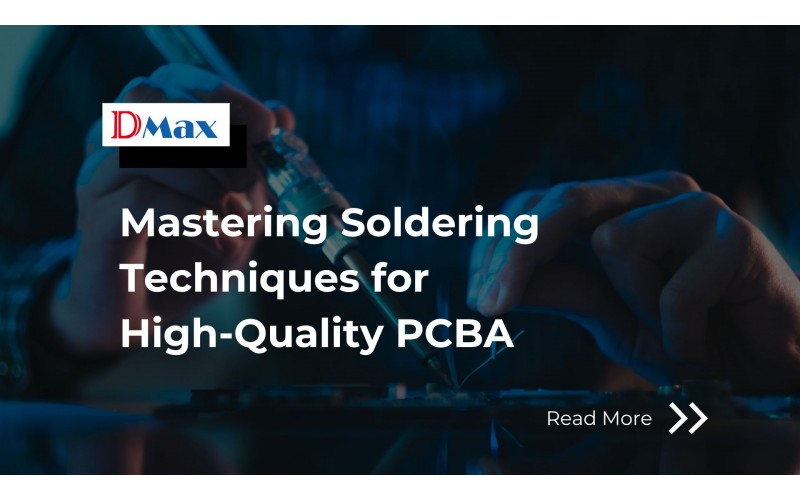
-
2025Feb
-
Soldering Techniques in PCBA Manufacturing
Why Is Soldering Important in PCBA?
Soldering forms strong, conductive connections between electronic components and the PCB, enabling efficient signal transmission and mechanical stability. Poor soldering can lead to defective joints, signal interference, and even device failure.
As miniaturization and high-density PCB assembly (like HDI PCB manufacturing) become more prevalent, precision soldering techniques are essential for fine-pitch components and advanced PCBA designs.
Common Soldering Techniques in PCBA Manufacturing
1. Reflow Soldering (Most Common for SMT Components)
Reflow soldering is the most widely used technique in Surface Mount Technology (SMT) assembly, ensuring efficient mass production with high precision.
✅ Process Overview:
-
Solder paste application: A stencil deposits solder paste onto PCB pads.
-
Component placement: SMT components are precisely positioned using pick-and-place machines.
-
Reflow oven heating: The PCB passes through controlled temperature zones, melting the solder and forming strong electrical connections.
✅ Advantages:
-
High-speed, cost-effective for mass production
-
Precise and reliable for fine-pitch components
-
Ensures uniform solder joints
✅ Applications:
-
Consumer electronics (smartphones, tablets, laptops)
-
HDI PCB manufacturing for compact, high-density boards
-
Automotive PCB and medical PCB applications
2. Wave Soldering (Best for Through-Hole Components)
Wave soldering is commonly used for Through-Hole Technology (THT), where components have leads inserted into PCB holes before soldering.
✅ Process Overview:
-
Flux application: The PCB is coated with flux to prevent oxidation.
-
Preheating: The PCB is heated to minimize thermal shock.
-
Solder wave contact: The PCB passes over a molten solder wave, which forms connections between the component leads and board.
✅ Advantages:
-
Ideal for THT components
-
Strong mechanical connections for high-stress environments
-
Cost-effective for high-volume production
✅ Applications:
-
Power electronics & industrial PCBs
-
Automotive PCBA with high mechanical stress
-
Military & aerospace applications requiring robust durability
3. Selective Soldering (Best for Mixed-Technology Boards)
Selective soldering is a more precise alternative to wave soldering, used when both SMT and THT components are present on a board.
✅ Process Overview:
-
Flux application: Flux is applied to specific areas needing soldering.
-
Preheating: The PCB is heated to avoid thermal stress.
-
Soldering nozzle application: A robotic nozzle deposits molten solder only on designated areas.
✅ Advantages:
-
Prevents thermal damage to sensitive SMT components
-
Reduces solder defects compared to wave soldering
-
Higher precision and lower solder waste
✅ Applications:
-
High-reliability PCBs (automotive, medical, aerospace)
-
PCB designs with a mix of SMT and THT components
4. Hand Soldering (For Prototyping & Repairs)
Hand soldering is used for low-volume production, prototyping, and rework/repairs.
✅ Process Overview:
-
A soldering iron is used to manually join components with solder wire.
✅ Advantages:
-
Ideal for small-scale assembly and prototype testing
-
Allows for manual adjustments and modifications
-
Useful for repairing defective solder joints
✅ Applications:
-
Prototype PCB assembly
-
Repairing damaged PCBs
-
Custom-built electronic projects
Key Factors Affecting Soldering Quality in PCBA
1️⃣ Solder Paste Composition: Lead-free vs. leaded solder options impact thermal properties and electrical conductivity.
2️⃣ Temperature Profile: Proper reflow oven temperature settings prevent cold joints and solder balling.
3️⃣ Flux Quality: Ensures clean surfaces, oxidation prevention, and strong solder adhesion.
4️⃣ Component Placement Accuracy: Poor alignment can cause open circuits and short circuits.
5️⃣ PCB Design Considerations: Proper pad spacing, via placement, and solder mask application improve solderability.
Choosing the Right Soldering Technique for Your PCBA
The best soldering method depends on component type, production scale, and application requirements:
Soldering Method
Best For
Common Applications
Reflow Soldering
SMT components
Smartphones, HDI PCBs, IoT devices
Wave Soldering
Through-hole components
Automotive PCBs, industrial electronics
Selective Soldering
Mixed SMT & THT boards
Aerospace, medical electronics
Hand Soldering
Prototyping & repair
Low-volume production, PCB rework
For mass production, automated soldering techniques (reflow & wave soldering) ensure high consistency and efficiency. For complex PCB designs, selective soldering is preferable.
FAQs on PCBA Soldering Techniques
❓ What is the best soldering method for HDI PCBs?
✔️ Reflow soldering is preferred for fine-pitch HDI PCB components.
❓ How does soldering quality impact PCBA reliability?
✔️ Poor soldering leads to cold joints, cracks, and electrical failures, reducing product lifespan.
❓ What are common soldering defects in PCBA manufacturing?
✔️ Solder bridging, cold joints, insufficient wetting, and voids can impact PCBA functionality.
❓ Is lead-free solder better than leaded solder?
✔️ Lead-free solder is RoHS-compliant but has a higher melting point, requiring optimized reflow profiles.
Conclusion: Optimizing PCBA Soldering for High-Quality Assembly
Choosing the right soldering technique is crucial for high-quality PCBA manufacturing. Whether using reflow, wave, selective, or hand soldering, optimizing temperature control, solder material, and process precision ensures strong, reliable, and defect-free solder joints.
For businesses requiring high-performance PCBA solutions, partnering with a professional EMS provider ensures superior soldering quality, efficient production, and long-term reliability.
Would you like additional insights on soldering defect troubleshooting or process optimization? Let me know!
-