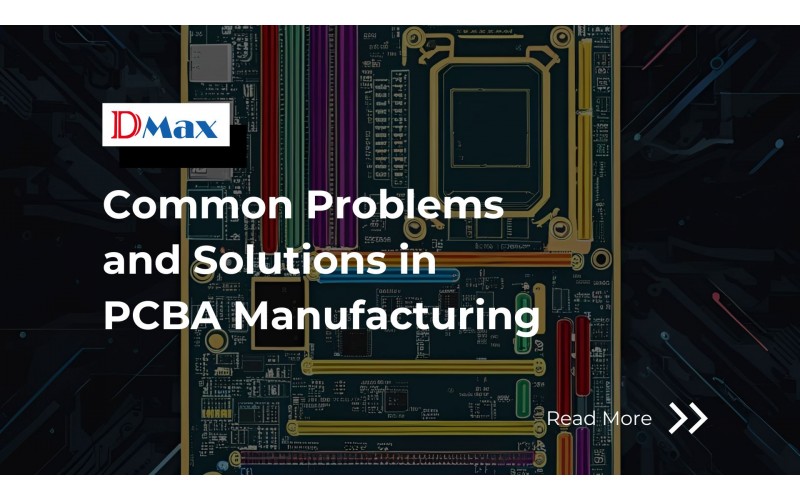
-
2025Mar
-
Common Problems and Solutions in PCBA Manufacturing
1. Soldering Defects
Problem: Cold Solder Joints
Cold solder joints occur when the solder does not properly bond with the components or PCB pads, often due to insufficient heat during reflow soldering. This results in weak electrical connections and potential failures.
Solution:
✅ Optimize reflow soldering temperature profiles
✅ Use high-quality solder paste with the correct flux composition
✅ Ensure proper PCB preheating to promote even heat distribution
Problem: Solder Bridges
Solder bridges happen when excess solder forms unintended connections between adjacent pads, causing short circuits. This is a common issue in fine-pitch components and BGA packages.
Solution:
✅ Adjust solder paste stencil design to prevent excess paste deposition
✅ Improve pick-and-place accuracy to ensure correct component positioning
✅ Utilize Automated Optical Inspection (AOI) and X-ray Inspection (AXI) to detect defects
2. Component Placement Issues
Problem: Tombstoning (Manhattan Effect)
Tombstoning occurs when one side of a small Surface Mount Device (SMD) lifts off the PCB during reflow soldering, resembling a standing tombstone. This happens due to uneven heating or solder tension imbalance.
Solution:
✅ Ensure balanced pad sizes and symmetric layout for small components
✅ Optimize the reflow oven's temperature profile to prevent uneven heating
✅ Use low-tension solder paste to minimize pulling forces
Problem: Misaligned or Missing Components**
Misaligned components can result from inaccurate pick-and-place machines or excessive vibration during handling. Missing components, on the other hand, may be due to feeding errors or weak adhesion before soldering.
Solution:
✅ Regularly calibrate pick-and-place equipment for accuracy
✅ Use vacuum-based component pick-up for secure placement
✅ Implement AOI inspections before reflow soldering to catch misplacements early
3. PCB Design & Layout Errors
Problem: Poor Signal Integrity (SI) & Electromagnetic Interference (EMI)**
PCB layout plays a critical role in maintaining signal integrity and preventing EMI issues. Improper routing of high-speed signals can lead to cross-talk, noise, and performance degradation.
Solution:
✅ Use proper ground plane design to minimize interference
✅ Optimize trace routing for differential signals and high-speed components
✅ Maintain adequate spacing between high-frequency and power traces
Problem: Thermal Issues & Overheating**
Heat dissipation is essential in high-power and dense PCBA designs. Overheating can cause premature component failures and affect board reliability.
Solution:
✅ Utilize thermal vias and heat sinks to dissipate excess heat
✅ Implement copper pours in high-power sections to distribute thermal load
✅ Choose components with higher thermal tolerance
4. PCB Contamination & Reliability Issues
Problem: Flux Residue & Contaminants**
Leftover flux or contaminants on the PCB surface can cause electrical leakage, corrosion, and adhesion issues.
Solution:
✅ Use automated PCB cleaning systems to remove flux and residues
✅ Apply no-clean flux when possible to minimize post-soldering cleaning
✅ Maintain a clean and controlled manufacturing environment
Problem: Board Warpage & Mechanical Stress**
PCB warping can occur due to uneven copper distribution, excessive thermal stress, or improper handling. This can lead to assembly difficulties and reliability issues.
Solution:
✅ Use balanced layer stack-ups to minimize warpage
✅ Control reflow temperature profiles to reduce thermal shock
✅ Store PCBs in humidity-controlled environments
5. Electrical Testing Failures
Problem: Open Circuits & Short Circuits**
Open circuits prevent current flow due to broken traces or poor solder joints, while short circuits can cause catastrophic failures.
Solution:
✅ Implement In-Circuit Testing (ICT) to catch electrical faults early
✅ Use Flying Probe Testing (FPT) for prototypes and low-volume runs
✅ Perform Functional Testing (FCT) to validate the final product’s performance
Problem: Insufficient Board-Level Testing**
Some failures may not be immediately detectable and only arise after real-world operation.
Solution:
✅ Conduct Burn-in Testing for high-reliability applications
✅ Perform stress and environmental testing for industrial and automotive PCBAs
✅ Ensure compliance with IPC-A-610 standards for PCB assembly quality
Final Thoughts: Preventing PCBA Manufacturing Defects
Minimizing defects in PCBA manufacturing requires a combination of design best practices, precision equipment, and quality control measures. By addressing soldering issues, component placement challenges, PCB layout concerns, and testing limitations, manufacturers can enhance product reliability and performance.